
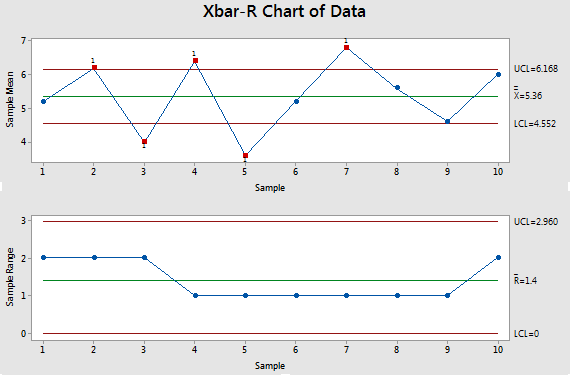
(Note that these defaults will apply to Individuals and X-bar charts. SigmaXL > Control Charts > “Tests for Special Causes” Defaults to run selected tests for special causes. Test 2 can be set to 7, 8, or 9 points in a row on same side of CL. The tests for special causes can have defaults set to apply any or all of Tests 1-8.Note that the Range chart is in-control even though the X-Bar chart is out-of-control: The use of tests for special causes gave us an early warning of this at observation number 22. In this case, the assignable cause was a change of rubber band requiring a reset of the pull back angle. The process must be stopped, and the Out-of-Control Action Plan must be followed to determine and fix the root cause. Tests for Special Causes report clearly shows that this process is now out of control with an unstable mean. Tests for Special Causes report gives us more detail on the recent instability: The X-bar chart and Recalculated when a deliberate process change or improvement is Once control limits are established, they should only be Note that the Add Data button does NOT recalculate the control SigmaXL Chart Tools > Add Data to this Control Chart as shown. To add the additional data to this chart, click Subgroups 21 to 25 were added afterwards. This is currently a stable catapult process.Operator, click Optional X-Axis Labels >. Shot 2, Shot 3, click Numeric Data Variables (Y) > select Select B2:F22 here, we will only use the first 20 subgroups to determine the control limits.The Lower Specification Limit (LSL) is 92 inches. The Upper Specification Limit (USL) is 108 inches. Open the file Catapult Data – Xbar Control Charts.xlsx.→ For better understanding refer below picture which is very easy to understand with the help of classification. ⇢ Focus on defects (occurrence) or defectives (pieces or units) ⇢ The number of samples is available in each subgroup or we can say subgroup size. ⇢ Nature of recorded data type such as variable or attribute → The classification depends on the below parameters. → There are many types of control_charts are available in Statistical Process_Control. Weight, Height, Length, Hardness, Diameter, Angle ⇢ Attribute data that can be counted or can give an answer in Go/No Go, OK/Not OK or Pass/Fail → There are two types - Attribute and Variable ➝ "Special cause is caused by known factors that result in a non-random distribution of output" the rubbing effect of matting part like gears, bearings, etc.

➝ "Common cause is fluctuation caused by unknown factors resulting in a steady but random distribution of output around the average of the data." ➝ Action entirely depends on the type of cause identified. ➝ Two types of causes are responsible for the variation.
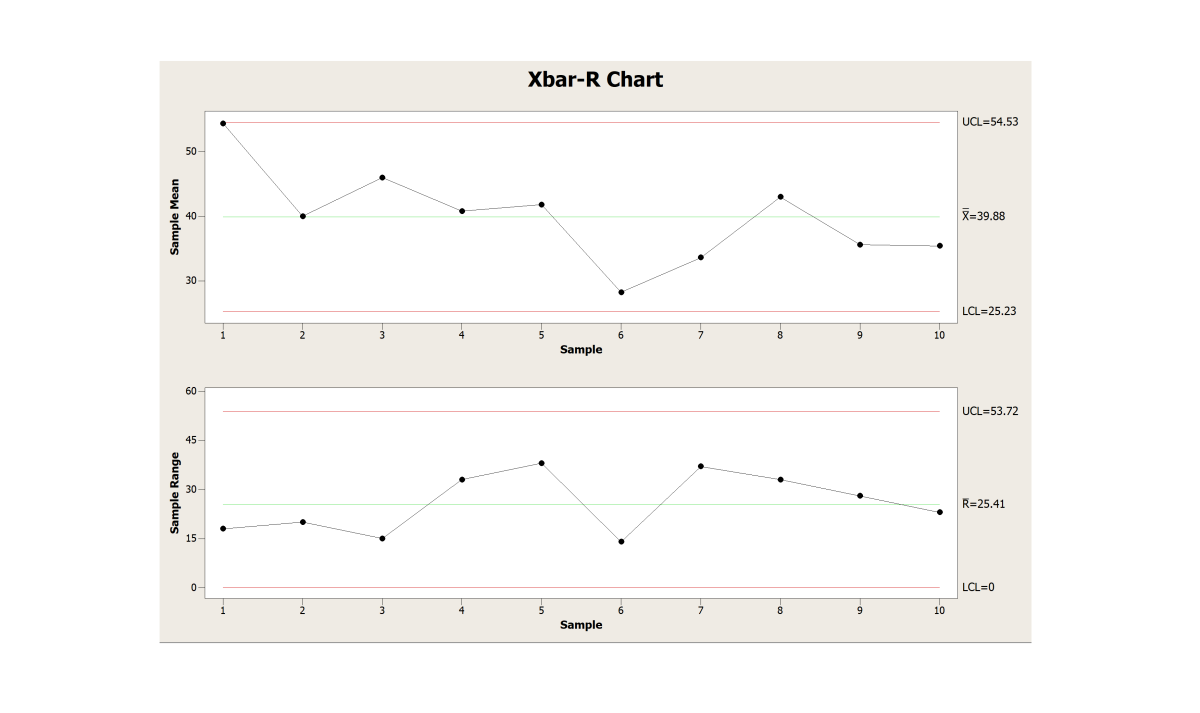
➝ More the variation, the more loss to the Organization. ➝ By 1920, the engineers had already realized the importance of reducing variation in the manufacturing operation. ➝ Because amplifiers and other equipment had to be buried underground, there was a stronger business needs to reduce the frequency of failures and repairs. ➝ The company's engineers had been seeking to improve the reliability of their telephony transmission systems. ➝ So this is called "Shewhart Control_Charts". Shewhart working for Bell Labs in the 1920s.
